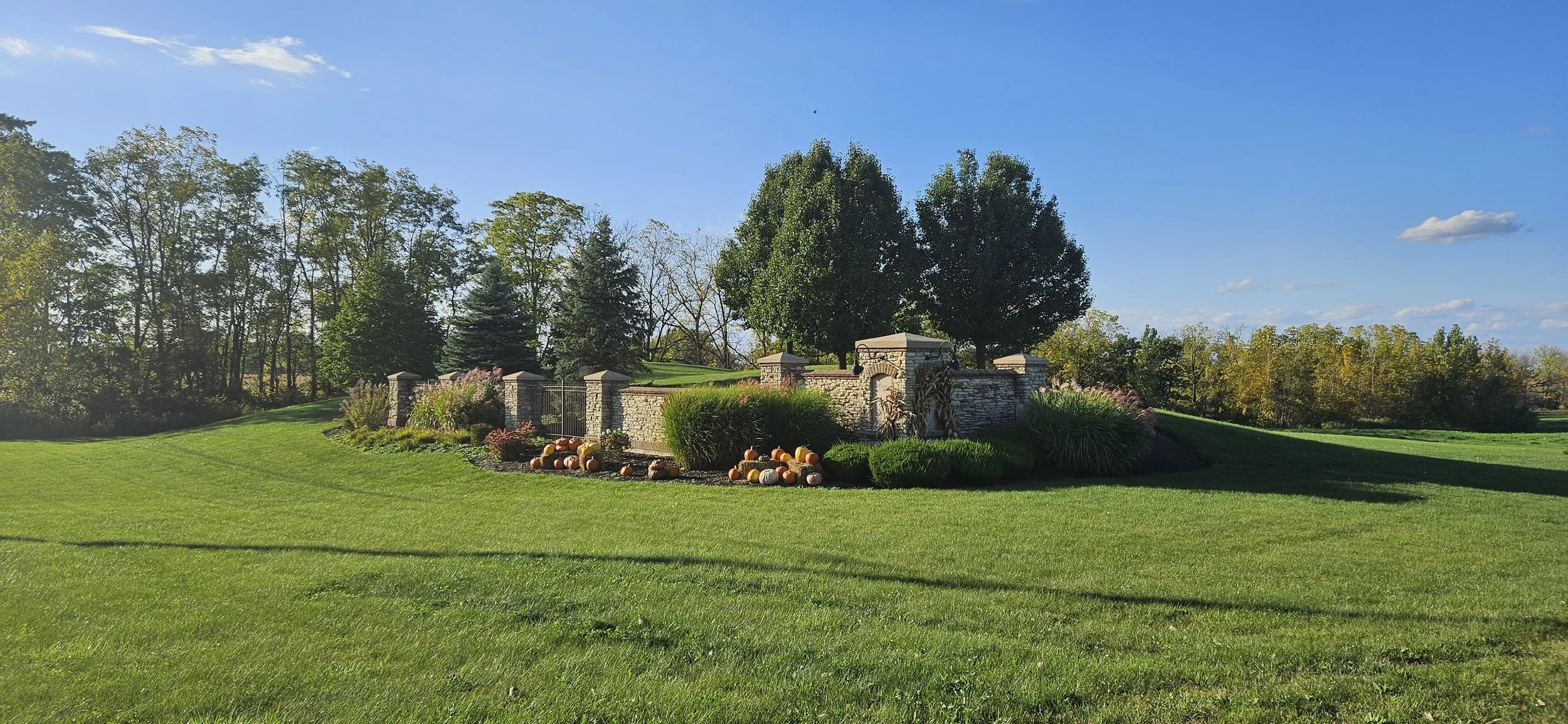
The Hennings Subdivision is a community of semi-custom ranch homes that is located a half-mile to the east of the intersection of U.S. Route 20 (Grant Highway) and Church Road in Huntley, Illinois. The community has convenient access east to Chicago and its suburbs or west towards Rockford via Interstate 90 which is approximately three miles away.
All homesites are served by paved roads maintained by the local township. A community-based sanitary sewer collection system is installed throughout the subdivision. Sanitary wastewater is treated on-site by the HOA’s Wastewater Reclamation and Reuse System. Private wells provide potable water to all homesites. Underground electric, natural gas, telephone, and cable services have been installed to most lots.
Available homesites for sale include select 1/3-acre (Hennings East) and one-acre homesites (Hennings West). All homesites overlook large amounts of open spaces, native prairies, mature woods, and numerous stormwater drainage ponds.
About Our Builder
Seven5 LLC is a distinguished investment and construction management firm headquartered in the Northwest suburbs of Chicago. With over 25 years of experience, they specialize in bringing top-quality, commercial, and residential projects to life. Their comprehensive services encompass new construction and renovations, all delivered with a commitment to personalized attention and professional excellence that consistently surpasses their clients’ expectations.
A Brief History of The Hennings Subdivision:
Years 2009-2016: Subdivision plan for 125 homesites is approved by McHenry County as the subdivision called Henning Estates. Roughly 19 homes are built and sold on 1/3-acre sites by the original developer.
Years 2018-2019: The original developer sends notice that he’s quitting the business and abandons Hennings Estates. Developer caretakes the subdivision until they are able to sell the entire property to another builder. An advisory board of four homeowners is established to maintain ongoing operations of the subdivision after the developer declares bankruptcy. The developer's ~$600K Letter of Credit (LoC) is transferred to McHenry County.
Year 2020: Coral Township takes over management, operation, and maintenance of the subdivision’s roads. The Advisory Board sells four partially completed/abandoned houses to a new builder to add to the subdivision. McHenry County hires an engineering firm to assess subdivision’s priorities using the LoC funding.
Year 2021: Members of prior Advisory Board are now elected as first Hennings Subdivision HOA Board. Residents sign a legal agreement with the now-bankrupt developer to assume ownership of all unsold/undeveloped subdivision lots.
Year 2022: HOA Board updates its Declaration of Covenants which are approved by 2/3 of all Owners. McHenry County issues subcontracts to use the LoC funds to complete unfinished work within subdivision. Contractors start work on completing LoC tasks under management by McHenry County.
Year 2023: The HOA Board entered into an agreement with a real estate broker to market up to 57 home sites that the HOA currently owns to qualified builder/developers.
Year 2024: The Hennings Subdivision Homeowners Association (HSHOA) has entered into an agreement with Seven5 Builders LLC to construct new ranch-style custom homes on 19 undeveloped lots that the HOA currently owns.
The Subdivision’s Goals
Maintain the high quality and value of all the subdivision’s homes using the HOA’s Declaration of Covenants.
Operate and maintain our private Waste-Water Reuse & Recycle System at the lowest possible cost to Owners.
Manage and enhance the subdivision’s native prairie plantings consistent with McHenry County guidelines.
Encourage all Owners to actively participate in managing the sustainability of the entire subdivision.
HOA Board of Directors
Develop and manage the annual budget.
Act in a fiduciary manner to protect the interests of the HOA.
Interact directly with the HOA’s attorneys and accountants.
Manage the subdivision’s stormwater and wastewater infrastructure.
Listen and respond to Owner questions and concerns.
Balance maintenance of open spaces while promoting future land development.
Conduct quarterly Board meetings and attend other task or strategic meetings.
Communicate with local officials on policies that could affect the subdivision.
Coordinate with community policing to promote neighborhood security.
Architectural Committee
Provide homeowner guidance using the HOA’s Covenants regarding exterior home modifications.
Provide builder guidance using the HOA’s Covenants regarding new house construction.
Submit recommendations to the Board of Directors for final approval of exterior home modifications or new home construction.
Landscape Committee
Identifies annual common area landscaping maintenance and improvements.
Solicits quotes from qualified/insured contractors for both price and performance.
Creates an annual operating budget and submits same to Board for consideration and approval.
Solicits volunteers for specific landscaping maintenance and improvements.
Subdivision Focus Group
Solicit input from all Owners regarding their vision of the future of The Hennings Subdivision.
Ensure that the subdivision’s high-quality standards for new home construction are conveyed to prospective builders.
Receive input from Owners regarding adding future amenities that could add to the subdivision’s value.
Wastewater Reclamation and Reuse System
Developed over the course of the last three decades, Sheaffer & Roland’s Wastewater Reclamation and Reuse System (WWRRS) provides an environmentally sensitive and odor-free approach to wastewater management. In this system, the wastewater is first reclaimed in deep aerated cells, followed by filtration and disinfection. The product is reclaimed water which is reused to irrigate and fertilize agricultural crops, landscape vegetation or recreational turf. It is applied at a rate consistent with plant needs, climatic environment, and soil conditions. When wastewater is reclaimed and reused there is no effluent disposal or discharge site. Rather, there is a utilization site where reclaimed, pathogen-free water containing basic plant nutrients like nitrogen, phosphorous and potassium are used to irrigate and fertilize growing plants. The water is cleansed further by the living filter of plants, soil, and geology to help to recharge local groundwater supplies.
Elements of the Deep Cell WWRRS
The following elements typically comprise the treatment and reuse train for a deep-cell WWRRS in an urban setting as designed by Sheaffer & Roland, Inc. (S&R).
The comminutor grinds up sewage solids before the wastewater enters the aerated cells. The comminutor is covered to prevent odors.
There usually are two deep aerated treatment cells with a total retention time of two to five weeks. Wastewater enters at the bottom of the aerated cells to prevent odors. The cells are designed to allow for the settling of solids, which collect in the containment area where final decomposition occurs. The small volume of residual solids may be removed once every 20-40 years.
Storage reservoirs provide reclaimed water during cold weather, precipitation, or other non-irrigation periods.
Filtration increases the efficiency of the disinfection process (see below) and minimizes clogging of irrigation equipment. It is not needed for agricultural irrigation. Intermittent slow rate sand filters or gravity sand filters normally are used.
Disinfection is commonly used in situations where there is a high degree of human activity in the irrigation area such as with golf courses, public parks, sports fields or other recreation or picnic areas. Disinfection is typically accomplished by chlorination.
The Operations Building is a small structure that houses the air blowers, all electrical controls, telemetry equipment, and disinfection equipment.
Public Health Aspects of the S&R WWRRS
Within the S&R design, aggressive aeration - along with filtration, disinfection, and redundancy - provide the highest level of protection against potential public health problems. The resulting high level of purity presents no threat to human contact. The following treatment processes are part of S&R’s system:
More than a month's total detention in the aerated treatment cells.
Up to 150 days of retention in the storage reservoir also provides for significant pathogen reduction.
Sand further assures removal of suspended solids and to break up biological "clumps" prior to disinfection.
Chlorination assures a pathogen-free irrigation water supply.
Odors in Wastewater Treatment Processes
Under certain conditions, offensive odors are produced when organic compounds decompose and are exposed to the atmosphere. Odors are prevented in the S&R exclusive deep-cell system under nearly all conditions.
Untreated sewage is not exposed to the surface; it is introduced near the bottom of the cell, where it is covered by from 15 to 25 feet of heavily aerated water. During the ongoing treatment process the organics are decomposed by oxidation.
The residual solids are deposited on the bottom in a storage area where the remaining organics decompose in the absence of oxygen (anaerobically) for years. The S&R system is designed so that even under highly variable wastewater flows and characteristics there will be no difference in treatment effectiveness.
Reserve aeration capacity is just one of the keys to this quality. S&R systems solve the sludge odor issue by not producing sludge in the first place. Thus, unlike conventional sewage treatment plants that produce sludge which must be removed as part of their regular operation, there simply are no odors associated with sludge removal.